Class Schedule
We are finding that the liability insurance for holding classes is prohibitive. We are told that our house insurance will be over double its present cost. There will also be a charge for liability for the studio itself which will run over a thousand dollars. Therefore, while we are still looking into the costs most likely we will not hold classes since the insurance may cost more than can be earned by teaching classes.
Instead of classes I will just work on my own pottery. I sit and throw bowls and plates while listening to music. I am working with multiple glaze combination which is very artistic and quite a bit of fun. It is very peaceful.
If the cost of insurance changes then we will reconsider. We are told that since the pandemic and the fires in California insurance companies are tightening the underwriting to cover their cost and most likely to make as large a profit as they can. It is too bad because I enjoyed teaching pottery and it is a lot of fun for those taking the classes. As one agent said the companies seem to be trying to take the fun out of life.
Topics that could be covered in classes
Hand building and wheel throwing
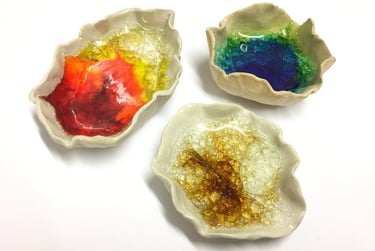
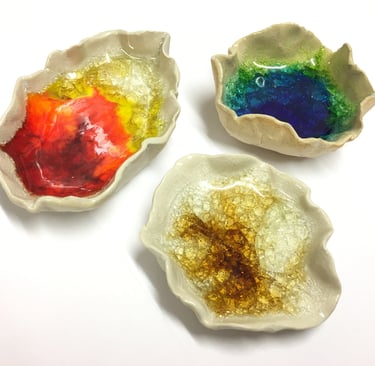
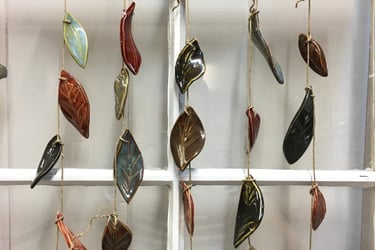
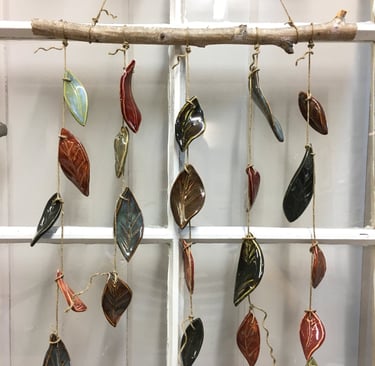
The above are images of student work from prior years. They include slab rolled, wheel thrown, and hand built pieces. We have found that students enjoy slab rolling and hand building more than wheel throwing. Wheel throwing takes a lot of practice. We have three potter's wheels for those who want to work with wheel throwing. We sold three other wheels as we reduced the size of the wheel throwing area. No one was using the wheels, everyone was hand building. We also have devices to make it easier to wheel throw such as the strong arm device that makes centering and opening easier. It takes the place of strong muscles in the arm. We have slab rollers and extruders that make hand building fun and easy. We have hundreds of glazes and underglazes. The pattern in the first image above left, bowl in center, was done with underglazes. We use commercial glazes and underglazes since there is a very large variety of glazes available and they are easier for students to use. Commercial glazes are also food safe and labeled that way.
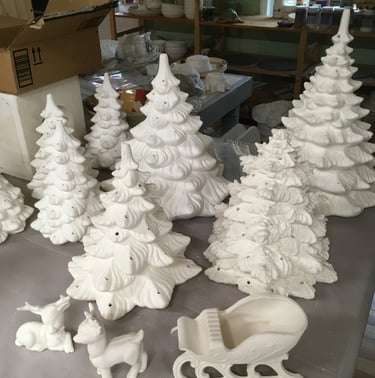
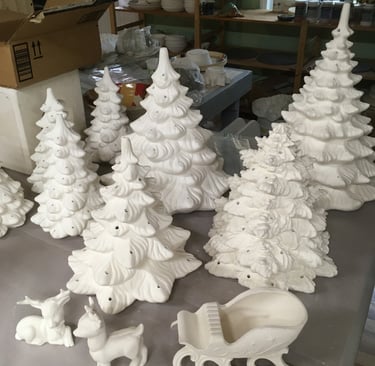
Slip Casting
Slip casting is a technique that uses a liquid clay solution called slip to cast a shape such as a tree using a plaster mold. The piece is then partially dried in the mold, removed from the mold, trimmed, left to dry again, bisque fired, glazed, and glaze fired. Plaster molds absorb water from the slip leaving a partially dried covering over the inside of the mold. That covering is generally about 1/8 of an inch thick or slightly thicker. The liquid slip inside of the mold is then poured out leaving the thin layer of partially dried clay in the mold. That layer is then left to dry until the mold can be removed leaving the internal partially dry shape intact. The piece is then trimmed so that it is ready to be fired in the kiln. The fired shape is called bisque. The bisque is glazed with glazes both colored and clear. It is then fired to become the finished piece.
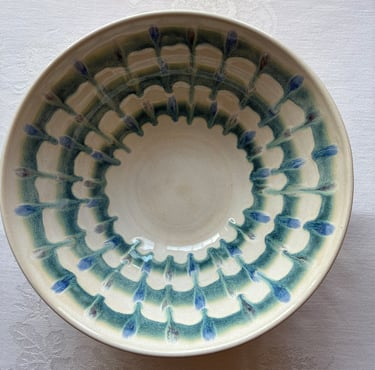
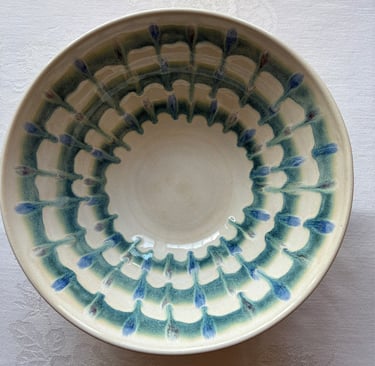
Glazing Techniques for Stoneware
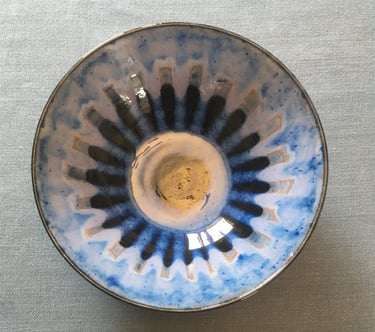
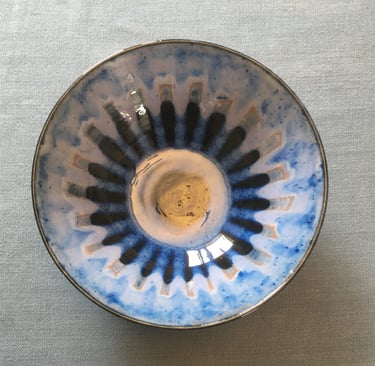
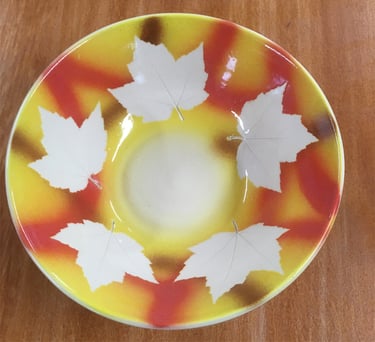
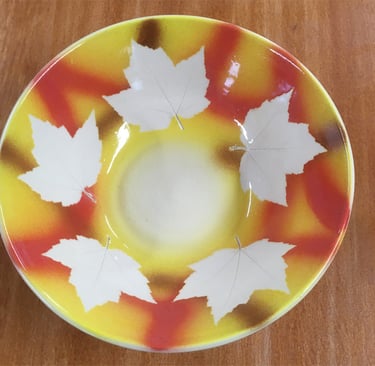
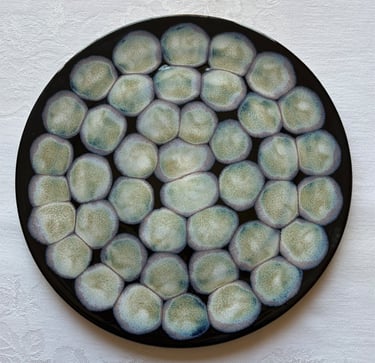
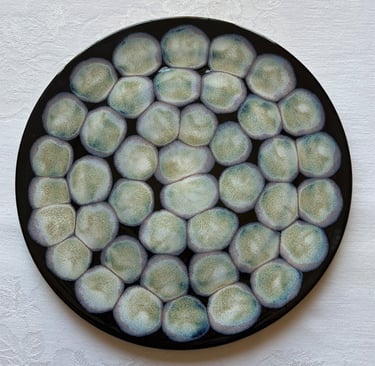
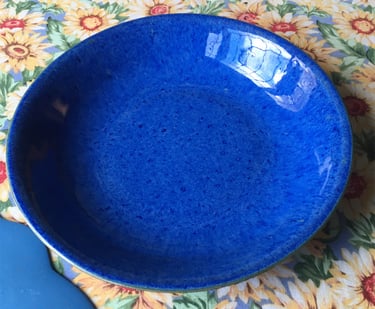
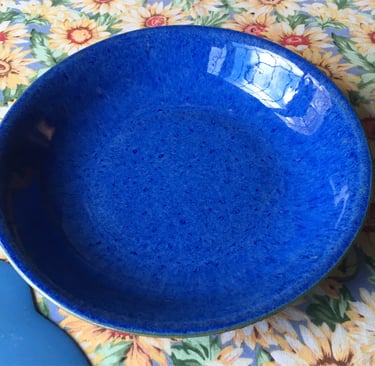
In the past potters made their own glazes. Eventually over the last 20 years commercial glazes developed a wide variety of colors and characteristics that have made potters go wild with their techniques. Being retired I have had the time to try many commercials glazes and many techniques. It is simply fun to try various techniques: brightly colored glazes, translucent glazes, glaze layering, glaze combinations, flux glazes that run, underglazes, dipping glazes, spraying glazes, spit glazing, crazing glazes, glazes with large particles that melt during firing, peacock glazing, frozen pond glazing, confetti glazing, and on and on. Over the years pottery has become my way of relaxing. It can be the same for you. The glaze makes the piece.
Glazing Commercial Purchased or Studio Cast Earthenware Slip Bisque
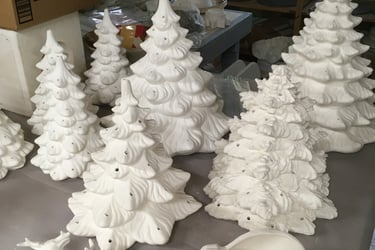
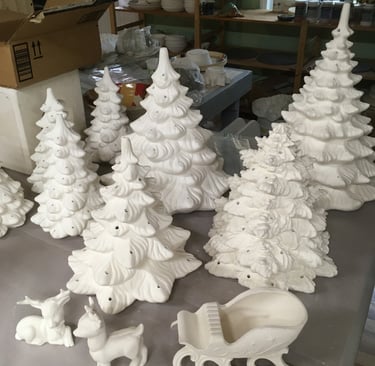
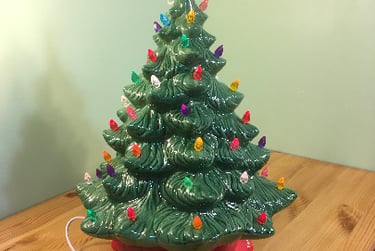
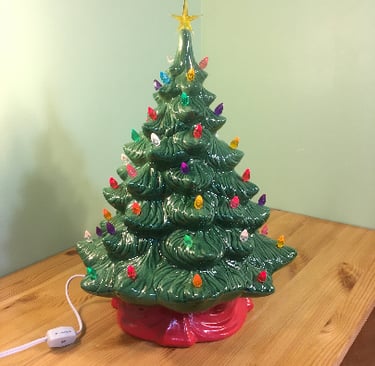
The above images are of finished pieces and bisque that students, both adults and children, have worked on in our studios. Pieces are painted with underglazes or glazes and then fired in our kilns. The first images are pieces done by a girl scout troop in our studios. The picture was taken right before the girls came to the studios to pick up their finished work. The two middle pictures are of bisque that is used for glaze and underglaze painting. The last picture is of a finished 17 inch Christmas tree with lights that shine from the light bulb inside the tree. Bisque is made using slip casting. We have two slip casting machines and purchase bisque pieces from Gare a bisque supplier.
Contacts
donaldjoy@joyceramics.com
(413) 768-1229